The Crucial Role of an Oil Seal Factory in Diesel Engine Parts
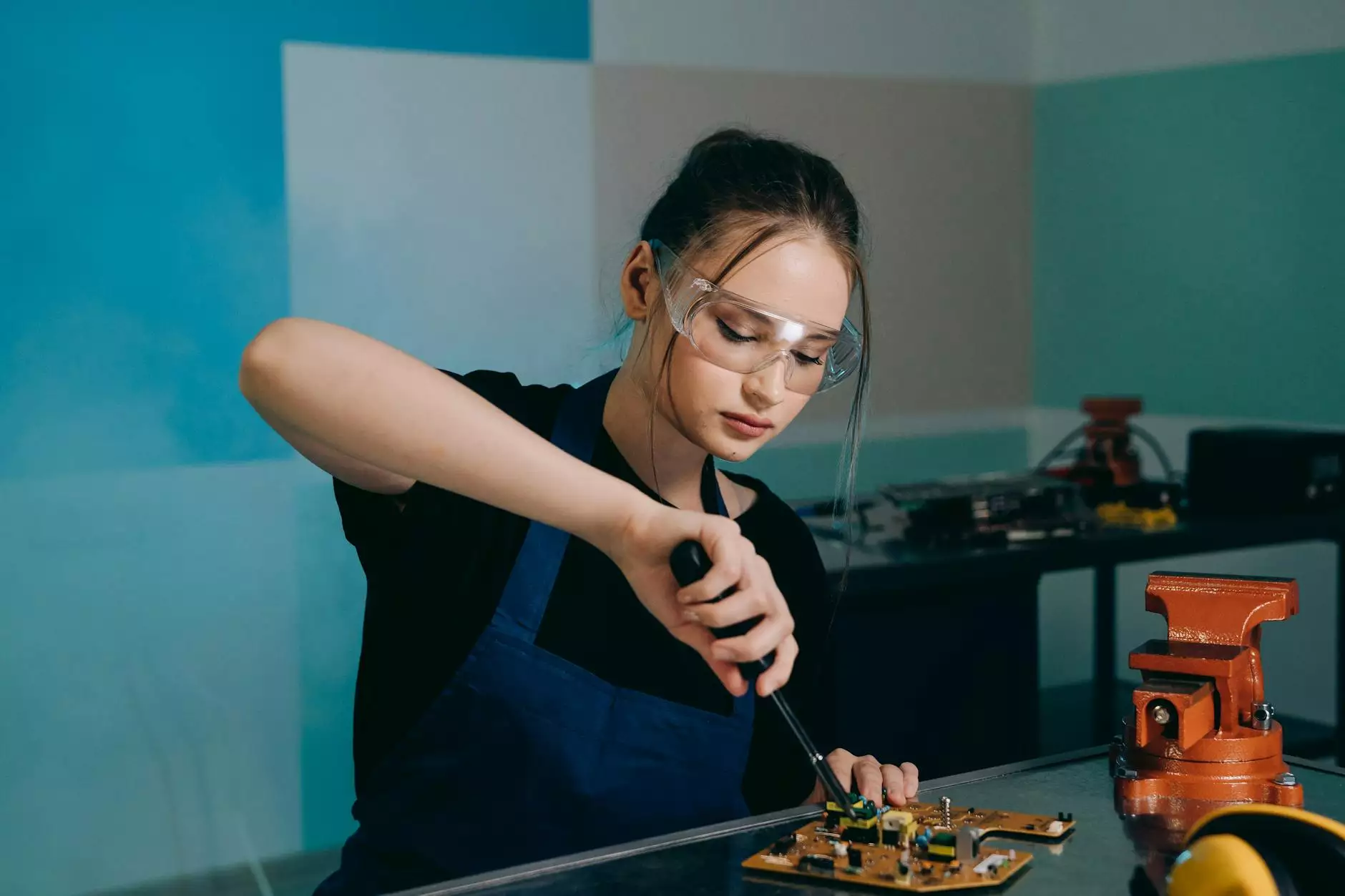
In today's fast-paced industrial landscape, the production of high-quality diesel engine parts is vital for operational efficiency and long-lasting performance. Central to the effectiveness of these parts is the functionality of oil seals, which prevent leaks, protect components, and ensure smooth operation. This article delves into the world of oil seal factories, highlighting their importance, the manufacturing processes involved, and why they're indispensable in the spare parts supply chain.
Understanding Oil Seals: Essential Components for Diesel Engines
Oil seals are designed to create a barrier that prevents oil from leaking out and contaminants from entering critical engine components. These seals are used in various applications in diesel engines, including:
- Crankshaft seals: Protecting the engine from leaks and contamination.
- Timing cover seals: Ensuring that the timing mechanism operates without oil loss.
- Transmission seals: Maintaining fluid integrity in both manual and automatic transmissions.
The effectiveness of these seals directly impacts engine performance and longevity. Any failure in these components can lead to significant operational costs, making the role of a reliable oil seal factory critical.
The Manufacturing Process of Oil Seals
Producing oil seals involves several meticulous steps to ensure the highest quality product. Below is an overview of the typical manufacturing process:
1. Material Selection
The choice of materials is fundamental. Most oil seals are made from elastomers such as Nitrile (NBR), Fluoroelastomer (FKM), and Polyacrylate (ACM). These materials are chosen for their resistance to temperature, oil, and wear.
2. Design and Engineering
The next step involves intricate design and engineering. Oil seals must be precisely engineered to fit within specific tolerances. A good oil seal factory employs advanced CAD software to create accurate designs that meet specific engine requirements.
3. Molding and Production
Once designs are finalized, the production begins. The selected materials are molded into the desired shapes using thermal curing processes. This step is crucial, as the curing process ensures that the seals possess the required mechanical properties.
4. Quality Control
Quality assurance is a key aspect of oil seal manufacturing. Factories conduct various tests, including:
- Dimensional checks: Ensuring seals meet design specifications.
- Material testing: Assessing the durability and elasticity of the seals.
- Leak testing: Verifying the seals' effectiveness in preventing leaks.
Why Choose a Reliable Oil Seal Factory?
When businesses consider sourcing from an oil seal factory, they should prioritize established manufacturers that guarantee quality and reliability. Here are several reasons why selecting a top-tier factory is essential:
1. Consistency in Quality
High-quality manufacturers implement stringent quality control measures, ensuring that every batch of seals meets the established standards. This consistency is vital for companies relying on these parts for smooth operations.
2. Expertise and Experience
Experienced oil seal factories have a wealth of knowledge regarding material properties and manufacturing techniques. This expertise leads to better product designs and enhanced performance.
3. Comprehensive Support and Services
Reputable manufacturers often provide additional services, including technical support and custom engineering solutions tailored to specific applications. This support can significantly benefit businesses aiming for maximum efficiency.
Key Benefits of High-Quality Oil Seals for Diesel Engines
Investing in top-notch oil seals from a reliable factory can yield several benefits for diesel-engine applications:
1. Enhanced Performance
High-quality oil seals ensure optimal engine performance by minimizing leaks and ensuring proper lubrication. This is crucial for maintaining engine temperature and efficiency.
2. Reduced Maintenance Costs
With effective oil seals, the risk of engine damage is significantly reduced, leading to lower maintenance costs over time. Businesses can avoid costly repairs and replacements associated with oil leaks and related issues.
3. Increased Lifespan of Components
Quality oil seals contribute to the longevity of diesel engine components. By protecting critical areas from contaminants and maintaining oil integrity, these seals play a pivotal role in extending the lifespan of the entire engine.
Choosing the Right Oil Seal Factory: What to Look For
While many oil seal manufacturers exist, not all offer equal quality. Here are essential factors to consider when selecting an oil seal factory:
1. Industry Reputation
Research the manufacturer's reputation within the industry. Look for customer reviews, case studies, and testimonials that speak to the quality of their products and services.
2. Certification and Compliance
Ensure that the factory complies with relevant industry standards, such as ISO certifications. This compliance indicates that they follow stringent quality management systems.
3. Manufacturing Capabilities
Evaluate the factory's capabilities, including their product range, technological advancements in production, and ability to handle custom orders. A diverse manufacturing capability often translates to better product offerings.
4. Collaboration and Customer Service
A good oil seal factory will prioritize customer relationships, offering support and flexible collaboration options to ensure a seamless procurement process.
The Future of Oil Seal Manufacturing
The landscape of oil seal manufacturing is continuously evolving. Emerging trends and technologies are shaping the future of this vital industry:
1. Advancements in Material Science
Research into new materials that offer better resistance to harsh conditions and fluids will continue to improve oil seal performance and longevity.
2. Automation and Smart Manufacturing
Incorporating automation in production processes can enhance efficiency, reduce costs, and improve quality control measures.
3. Sustainable Practices
As industries push towards sustainability, oil seal factories will likely adopt eco-friendly materials and processes, focusing on reducing waste and minimizing their environmental impact.
Conclusion: Evolving Your Business with Quality Parts
In conclusion, the role of an oil seal factory in the production of diesel engine parts cannot be overstated. Quality oil seals enhance engine performance, reduce maintenance costs, and increase the longevity of critical components. By investing in seals from a credible factory such as those aligned with client-diesel.com, businesses can achieve operational excellence and ensure their diesel engines function at peak performance.
As the manufacturing landscape continues to evolve, staying abreast of advancements in oil seal technology and sourcing practices is crucial. Choose wisely, invest in quality, and watch your business thrive as a result of enhanced engine efficiency.