CNC Lathe Part Factory: Precision Manufacturing at Its Best
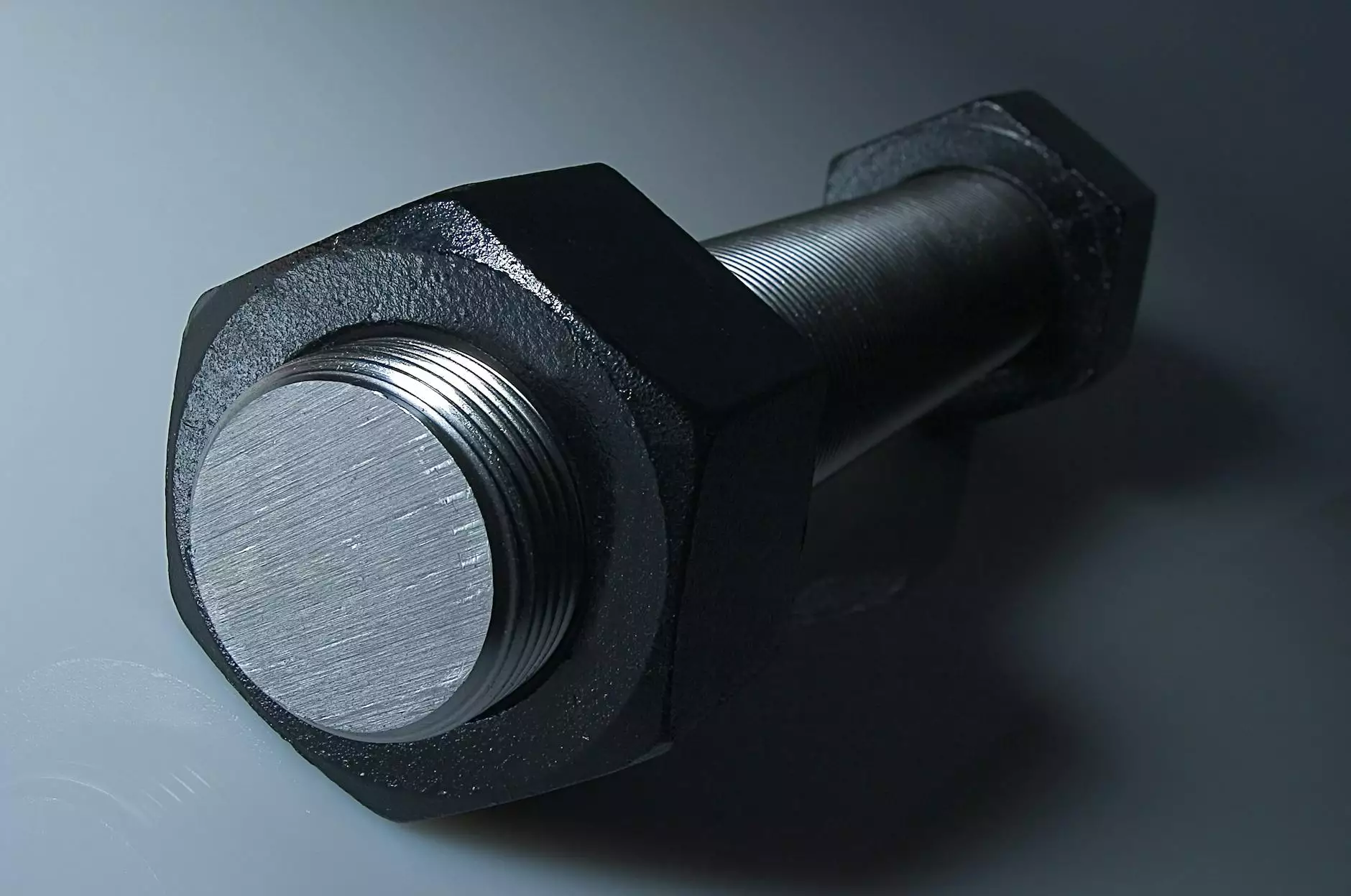
Understanding CNC Lathe Manufacturing
In the realm of modern manufacturing, the importance of precision and efficiency cannot be overstated. A CNC lathe part factory plays a crucial role in producing high-quality components that are integral to a multitude of industries, including automotive, aerospace, electronics, and more. Computer Numeric Control (CNC) lathes leverage advanced technology to accurately shape materials into specific designs, thereby ensuring consistency and reducing waste.
Why Choose CNC Machining?
CNC machining provides several advantages that set it apart from traditional manufacturing methods. Some key benefits include:
- Increased Precision: CNC machines operate using precise measurements programmed into the system, resulting in parts that meet exact specifications every time.
- High Efficiency: Automated processes lead to faster production times and the ability to scale operations according to demand.
- Versatility: CNC lathe machines can work with various materials, including metals, plastics, and composites, allowing for a wide range of applications.
- Consistency: Once programmed, CNC machines can replicate parts with minimal variation, ensuring uniformity across production runs.
- Complex Geometries: CNC lathes can produce intricate designs that would be challenging or impossible with manual methods.
The Production Process in a CNC Lathe Part Factory
The production process at a CNC lathe part factory involves several crucial stages, each designed to ensure the final product meets quality standards. Understanding these stages can help businesses appreciate how CNC machining can benefit them:
1. Design and Prototyping
The journey begins with designing the component, usually executed using Computer-Aided Design (CAD) software. This software allows engineers to create precise digital models of the part, facilitating thorough analysis before moving to the physical production phase.
2. Programming
Once the design is finalized, engineers convert it into a machine-readable format using Computer-Aided Manufacturing (CAM) software. This programming step involves specifying the cutting paths, speeds, and feeds that the CNC machine will follow.
3. Material Selection
Choosing the right material is critical for the performance and durability of the end product. CNC lathe part factories typically work with various materials, including:
- Aluminum
- Steel
- Copper
- Plastics
- Composites
Each material is selected based on the application and required material properties, ensuring optimal performance for the finished product.
4. Machining
The actual machining process involves securing the selected material on the CNC lathe and executing the programmed operations. The machine uses rotary tools to cut, shape, and refine the workpiece according to the precise specifications laid out in the design phase. This step typically produces very low waste, optimizing resource utilization.
5. Quality Control
Quality assurance is paramount in a CNC lathe part factory. After machining, parts undergo rigorous inspections to ensure they meet the required tolerances and specifications. Techniques including dimensional measurement using calipers or coordinated measuring machines (CMM) are employed to validate the part's accuracy.
6. Finishing
Depending on the application, finishing processes such as anodizing, plating, or polishing may be applied to enhance the appearance and corrosion resistance of the manufactured parts. This step is essential for components used in environments requiring superior durability.
Applications of CNC Lathe Parts
Components produced by CNC lathe part factories find applications in virtually every industry. Here are some notable sectors where CNC lathe parts are indispensable:
- Aerospace: Manufacturing lightweight and strong components for aircraft and spacecraft.
- Automotive: Producing engine components, bearings, and intricate parts for assembly lines.
- Medical: Manufacturing precision instrumentation and devices for healthcare.
- Electronics: Creating components for circuit boards and housings for electronic devices.
The versatility of CNC machining allows factories to cater to various industries, demonstrating the technology's wide-reaching impact.
Choosing the Right CNC Lathe Part Factory
Not all CNC lathe part factories are created equal. When selecting a manufacturing partner, businesses should consider several critical factors:
1. Expertise and Experience
Look for a factory with extensive experience in CNC machining. A knowledgeable team can provide valuable insights and improve the manufacturing process.
2. Quality Certifications
Ensure the factory holds relevant quality certifications, such as ISO 9001, which demonstrates a commitment to quality standards in manufacturing.
3. Technological Sophistication
A modern CNC lathe part factory should utilize the latest technology and machinery. State-of-the-art equipment often translates to better precision and reduced lead times.
4. Customization Options
The ability to customize components according to specific requirements is vital. A factory should be willing to collaborate on unique designs and adaptations to meet client needs.
5. Timely Delivery
Evaluate the factory's track record on delivery times. Meeting deadlines is crucial in maintaining production schedules and avoiding downtime.
The Future of CNC Lathe Manufacturing
As technology continues to advance, CNC lathe manufacturing is poised for transformative changes. Here are some trends shaping the future of CNC lathe part factories:
1. Increased Automation
The integration of robotics and AI into manufacturing processes promises to enhance efficiency further and reduce human error. Automated systems can manage repetitive tasks, allowing human workers to focus on more complex functions.
2. Advanced Materials
Research and development in material science are leading to the creation of new composites and alloys, which could open doors to manufacturing even more durable and lightweight components.
3. Sustainability
Environmental concerns are prompting many CNC lathe part factories to adopt more sustainable practices, such as using recycled materials and improving energy efficiency to reduce their carbon footprint.
4. Custom Manufacturing
The trend toward customization is expected to grow, with more manufacturers offering tailored production runs to accommodate specific client needs without sacrificing efficiency.
Conclusion
In the competitive landscape of manufacturing, partnering with a reputable CNC lathe part factory like DeepMould.net can provide businesses with a distinct advantage. The combination of precision engineering, advanced technology, and a commitment to quality ensures that your manufacturing needs are met with the highest standards. By understanding the benefits, processes, and future developments in CNC lathe manufacturing, organizations can better position themselves to thrive in today's dynamic market. Embrace the power of CNC machining and unlock new opportunities for innovation and growth.