Transforming the Automotive Industry with Plastic Injection Molding
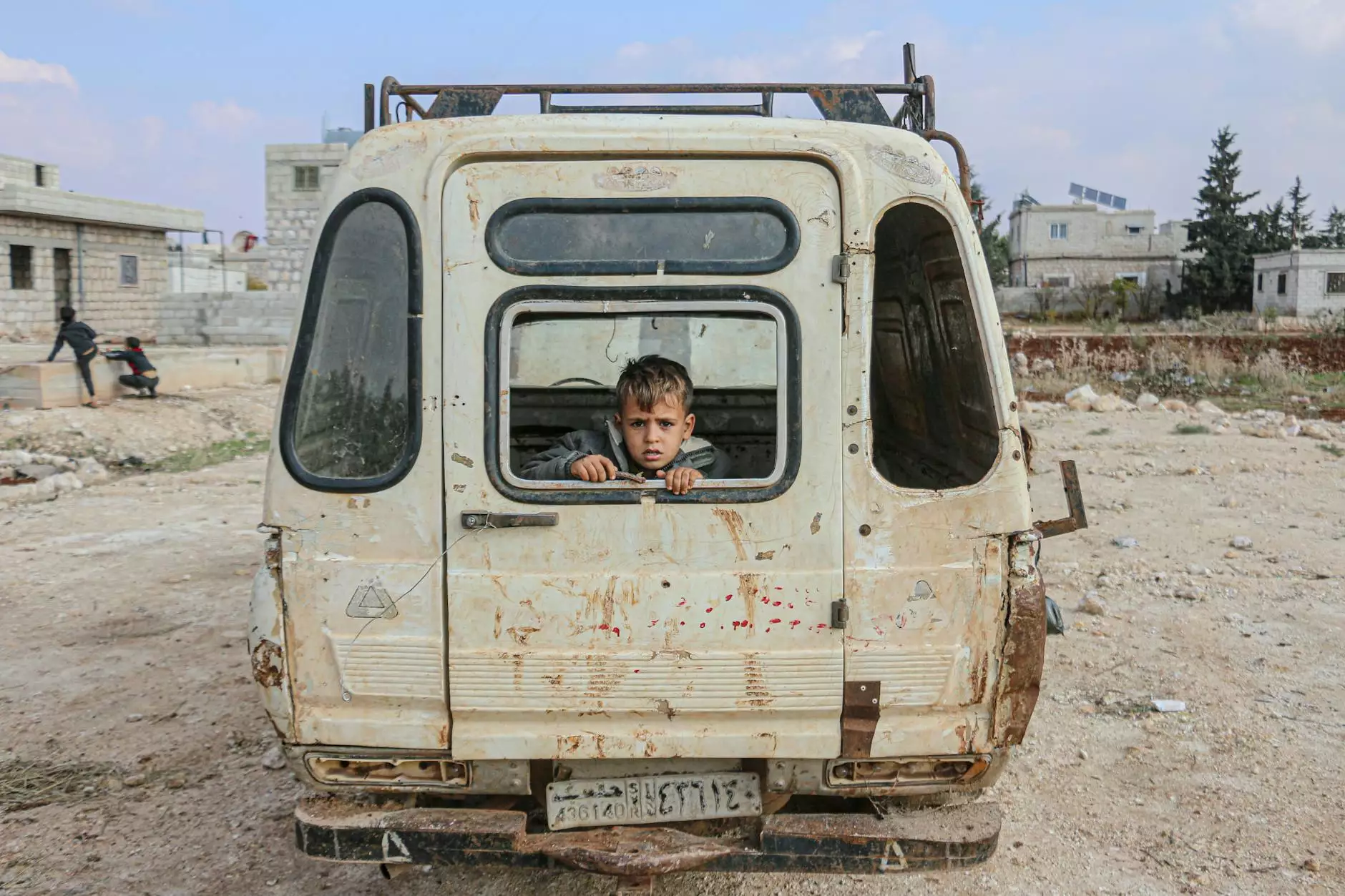
The automotive industry is a cornerstone of modern economies, continually evolving to meet consumer demands and regulatory standards. At the heart of this transformation are automotive plastic injection molding companies, playing a critical role in the production of various automotive components. In this article, we delve into the significance, processes, advantages, and key players in the realm of automotive plastic injection molding.
Understanding Plastic Injection Molding
Plastic injection molding is a manufacturing process for producing parts by injecting molten material into a mold. This process is particularly valuable in the automotive sector due to its efficiency, precision, and versatility.
The Injection Molding Process
The typical process of plastic injection molding involves several key steps:
- Material Selection: The right plastic material is selected, often depending on the required properties such as strength, durability, and weight.
- Mold Design: A mold is created, which is a hollow metal block that features the negative shape of the desired part.
- Injection: The plastic is heated until it becomes molten, then injected into the mold under high pressure.
- Cooling: The molten plastic cools and solidifies in the mold, taking on its shape.
- Demolding: Once cooled, the part is removed from the mold.
- Finishing: Additional processes may include trimming, painting, and assembly.
Why Choose Plastic Injection Molding for Automotive Parts?
Automotive plastic injection molding offers numerous benefits compared to traditional manufacturing methods. Here are a few compelling reasons:
- High Precision: Injection molding allows for highly precise and complex shapes, ensuring parts fit perfectly in assembly lines.
- Reduced Waste: The process minimizes material waste, as only the required amount of plastic is used for each part.
- Scalability: Once the mold is created, mass production can be carried out efficiently, significantly reducing per-unit costs.
- Versatility: A range of materials can be used, from ABS to polycarbonate, catering to different component requirements.
Leading Automotive Plastic Injection Molding Companies
Several automotive plastic injection molding companies have established themselves as industry champions, innovating and leading the way in high-quality production. Here are some of the most notable players:
1. DeepMould.net
DeepMould is a prominent name in the automotive plastic injection molding sector. With a focus on precision engineering and sustainable practices, DeepMould offers a wide range of services that cater specifically to the automotive industry, ensuring that each component meets rigorous quality standards.
2. Husky Injection Molding Systems
Husky is recognized for their innovation in injection molding technology. Their systems are engineered for high performance and efficiency, making them a preferred choice for automotive applications that demand both quality and speed.
3. Nypro, A Jabil Company
Nypro specializes in providing world-class manufacturing solutions. Their expertise in plastics helps automotive manufacturers reduce costs while maintaining high standards in production.
4. Continental Structural Plastics
Continental Structural Plastics focuses on lightweight composites and injection-molded parts, driving advancements in automotive design and efficiency.
Innovations in Injection Molding Technology
Continuous innovations in technology are shaping the future of automotive plastic injection molding companies. Here are key trends to watch:
1. Use of Advanced Materials
Incorporating advanced materials like thermoplastics and bio-based plastics enhances performance while adhering to environmental regulations.
2. Automation and Robotics
Automation is streamlining the injection molding process, improving efficiency and reducing labor costs. Robotic systems can handle tasks from machine operation to quality inspection.
3. Sustainability Practices
Sustainability is paramount in modern manufacturing. Many automotive plastic injection molding companies are adopting eco-friendly practices, such as optimizing energy consumption and recycling materials.
Challenges Faced by Automotive Plastic Injection Molding Companies
While the benefits are significant, there are challenges that these companies face:
- Tooling Costs: The initial investment in high-quality molds can be substantial.
- Material Handling: Managing different types of plastics and ensuring their proper processing can be complex.
- Meeting Standards: Automotive components must comply with stringent safety and quality standards, requiring rigorous testing and documentation.
Future of Automotive Plastic Injection Molding
The future looks promising for automotive plastic injection molding companies, particularly with the increasing push towards electric vehicles (EVs) and sustainable practices. As the automotive industry evolves, so too will the techniques and materials used in manufacturing. Companies that embrace innovation and sustainability will likely lead the way in this ever-competitive landscape.
Conclusion
The role of automotive plastic injection molding companies in shaping the future of automotive design and manufacturing cannot be understated. With their ability to produce high-quality, precise, and sustainable automotive components, they are crucial to the industry's ongoing evolution and success. By understanding the benefits, processes, and key players in this sector, stakeholders can make informed decisions that drive growth and innovation.